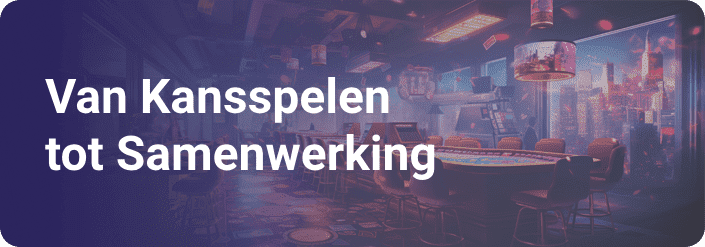
Inleiding
De gokindustrie is de afgelopen jaren snel gegroeid en heeft een aanzienlijke invloed uitgeoefend op de arbeidsmarkten wereldwijd. Deze groei heeft geleid tot onverwachte ontwikkelingen tussen verschillende regio’s in de wereld, waaronder de groeiende partnerschap tussen Kentucky en Nederland. Deze sectie onderzoekt de opkomst van de gokindustrie in Kentucky en de kenmerken van de relatie tussen deze staat en Nederland. Groei invloed van de gokindustrie op arbeidsmarkten. De wereldwijde gokmarkt heeft een aanzienlijke groei doorgemaakt. De waarde van de gokmarkt is in 2020 bijna $ 465,763.9 miljoen en wordt verwacht te bereiken $ 895,720.3 miljoen door 2030 . Met de groei van de gokindustrie groeit ook het aantal banen in de regio’s waar de gokindustrie bloeit. Onderzoeken laten zien dat de oprichting van casino’s het aantal banen in de regio doet toenemen, maar zulke vooruitgang zorgt niet altijd voor een hogere gemiddelde inkomsten . De gokindustrie is ook gunstig voor de economie van de staat dankzij de inkomsten en technologische vooruitgang die het stimuleert. Kentucky en Nederland. Ten iets interessants over de gokindustrie betreft Kentucky en Nederland. Andy Beshear, de gouverneur van Kentucky , heeft aangekondigt dat Kentucky en Nederland werkten samen in agritech en negen nieuwe leden hebben toegevoegd, inclusief zakenmensen uit bedrijven, overheid en onderwijs . De samenwerking tussen deze twee regio’s toont de onverwachte partnerschappen die kunnen worden verbrand door snel groeiende industrieën zoals gond en hoe ze ook invloed hebben op de gemaakt industrieën en technologie en onderwijssectoren. . Deze sectie heeft de invloed van de gokindustrie op in Kentucky en de effecten van de gokindustrie in Nederland gepresenteerd, evenals de unieke relatie tussen kentucky en Nederland. De volgende secties bevatten meer informatie over de gewenste aspecten.
De Banenmarkt in Kentucky: een Overzicht
Naast al deze industrieën staat Kentucky, een staat beroemd om zijn rijke tradities in paardenraces en bourbonproductie, bekend om zijn diverse en groeiende economie . Kentucky leidt in landbouw, waar het lokaal nationaal leidt in de productie van tabak en het een grote speler is in de vee- en graanproductie. Bovendien is de auto-industrie ook van cruciaal belang voor de economie, aangezien grote fabrieken van Ford, Toyota en General Motors duizenden werknemers in dienst hebben. De economie voortgestuwd door buitenlandse investeringen is even cruciaal voor de staat. Er zijn meer dan 500 buitenlandse bedrijven die in de staat actief zijn, en een groot deel daarvan zijn Japanse bedrijven. Dit draagt niet alleen bij aan de werkgelegenheid, maar ook aan de economische diversificatie . De sectoren waarin deze bedrijven actief zijn, lopen sterk uiteen, waaronder de automobielindustrie en chemische productie. Deze bedrijven bieden werk aan mensen met verschillende vaardigheden, variërend van productiewerk tot hooggespecialiseerde en technische beroepen. Deze diversiteit aan industrieën creëerde een diverse arbeidsmarkt die kansen biedt aan mensen met verschillende achtergronden. De staat bevordert buitenlandse investeringen door middel van belastingvrijstellingen en subsidies, waardoor arbeidsplaatsen verder worden gegeneerd. Buitenlandse investeringen hebben niet enkel directe banen gecreëerd, maar ook geleid tot de ontwikkeling van toeleveringsketens en dienstverlenende bedrijven in de staat, waardoor de economie groeit. Deze levendige arbeidsmarkt biedt kansen aan de inwoners van de staat, maar ook aan internationale arbeidskrachten. Het draagt bij aan de economische vitaliteit van de staat.
De Opkomst van de Gokindustrie in Nederland
Historische Ontwikkelingen en Huidige Context
De gokindustrie in Nederland is al rampzalig en duurt vele jaren . Het dateert voor de moderne regelgeving en wetgeving die het gokken op een veilige en controleerbare manier mogelijk maakt. De overheid heeft in de loop der jaren verschillende maatregelen genomen om de gok te reguleren, onder meer om consumenten te beschermen. Recentelijk werd de Wet Kansspelen op afstand , onder zijn andere naam de Wet Kansspelen op afstand , aangenomen in 2021 en grote veranderingen in de online gokwereld geïmplementeerd. De wet staat buitenlandse exploitanten toe om online casino’s te exploiteren die in Nederland moeten worden gelicentieerd. Dit verandert het spel aanzienlijk en de gokmarkt wordt veilig en eerlijk.
Wetgeving en Economische Gevolgen
Een van de meest onderscheidende veranderingen in de Nederlandse gokindustrie is de aanname van de Kansspelen op afstand enige jaren geleden. Het reguleert gokactiviteiten via het internet, beschermt spelers, voorkomt verslaving en fraude en stelt regels voor het verkrijgen van belastinginkomsten. Tot nu is de gokbelasting toegevoegd aan de begroting en het heeft een beslist positief effect op de nationale economie. Door de gok te legaliseren, kan de overheid belasting innen voor de gokinkomsten . Wijzigingen in de regelgeving stimuleren de concurrentie en creatievere aanbiedingen voor consumenten. Een ander voordeel van deze wet is het creëren van werkgelegenheid . De vraag naar het personeel in ploegendienst heeft geresulteerd in het huren van nog duizenden mensen.
Om samen te vatten, heeft de opkomst van de gokindustrie in Nederland, aangedreven door zowel historische als hedendaagse veranderingen, een grote invloed op de economie en maatschappij van Nederland. De huidige wetgeving op kansspelen op afstand speelt een cruciale rol in het creëren van een veilige regelgeving, die zowel economische kansen biedt als de consument beschermt.
Technologische Samenwerking: de Brug Tussen Kentucky en Nederland
De technologische samenwerking tussen Kentucky en Nederland is uitgegroeid tot een essentieel onderdeel van de relatie tussen de twee regio’s. De samenwerking wordt voornamelijk uitgevoerd in de agritech-sector en is gericht op de promotie van innovatie en duurzaamheid in de landbouw. Partners in de technologie: van paardenrace tot online gokken. De Kentucky-Netherlands Agritech Collaboration, waar negen nieuwe leden recentelijk aan zijn toegevoegd. Het partnerschap tussen de overheid, universiteiten en bedrijven van Kentucky en Nederland heeft tot doel agritech-innovaties te stimuleren. Kentucky en Nederland hebben kennis en technologie uitgewisseld die beide regio’s ten goede komt. Een ander voorbeeld is het Nederlandse high-tech tuinbouwbedrijf Bosch Growers dat voor Kentucky heeft gekozen. Deze illustratie toont toenemende Nederlandse interesse in de Amerikaanse markt en benadrukt de potentie voor extra samenwerking in geavanceerde landbouwtechnologie.
Exchange programs and joint ventures. De samenwerking omvat ook uitwisselingsprogramma’s en joint ventures met de focus op het ondersteunen van Nederlandse partners en publiek-private samenwerking met het tuinbouwcluster van Kentucky. Dit initiërend item door HAS International Projects ondersteunen de ontwikkeling van duurzame landbouw en technologische innovatie. De agritech-samenwerking tussen Kentucky en Nederland is een rolmodel voor hoe wereldwijde partnerschappen wederzijds voordelige resultaten kunnen opleveren. Door hun krachten te bundelen op het gebied van technologie en innovatie, bouwen Kentucky en Nederland samen aan een toekomst waar duurzaamheid en de toekomst hand in hand gaan.
Culturele en Economische Uitwisselingen
De interactie tussen de gokcultuur in Nederland en de staat Kentucky, Verenigde Staten (VS), heeft een boeiende culturele en economische uitwisseling gekend. Maar het verschilt niet alleen in de manier waarop gokken wordt bekeken in beide markten, het heeft ook een impact gehad in termen van de nieuwe markten en samenwerkingen die zich hebben ontwikkeld. Het effect dat de Nederlandse gokcultuur op Kentucky heeft gehad. De Nederlandse gokcultuur wordt doorgaans beschouwd als een van de meest liberale markten in de wereld van gokken. Kentucky heeft daarom ongetwijfeld een aantal van de beste regelgeving en consumentenbescherming van Nederland geleerd. Het heeft ze geholpen volwassener te worden en de nadruk te leggen op een beter hun spelers te beschermen en een eerlijk spel te bevorderen. Het effect van Kentucky gokkersmarktmogelijkheden in Nederland. Gezien het feit dat Kentucky een van de bekendste locaties in de Verenigde Staten is vanwege zijn paardenraces, kunnen we deze beschouwen als hun belangrijkste bijdrage aan de gokmarkt in Nederland. door hen geïnspireerd om hun aanbod te diversifiëren en met het brede publiek in interactie te treden. Hiermee kan Kentucky hun kennis delen van een vorm van weddenschappen die in Nederland algemeen bekend is. De wisselwerking tussen deze twee landen versterkt hun gokmarks maar helpt ook bij een grotere culturele uitwisseling. Er wordt immers samen gewerkt en deze kennis kan worden gebruikt om beide kanten van de industrie te verbeteren en de weg te wijzen naar andere samenwerkingsmogelijkheden. Dit betekent dat er potentieel is voor veel bedrijven in de gokindustrie om samen te werken en van elkaar te leren om nieuwe gokproducten en een veilige omgeving te ontwikkelen.
Sociale en economische gevolgen
De gokindustrie is zowel in Nederland als in Kentucky een belangrijke sociale en economische speler. Deze sectie bespreekt de impact van deze industrie op werkgelegenheid in beide regio’s, evenals bredere sociale kwesties en oplossingen. De werkgelegenheidseffecten zijn als volgt op beide regio’s: in Nederland heeft de legalisatie van online gokken de economie aangezwengeld, met een toename van de belastinginkomsten en de creatie van banen in de tech- en service-industrie. Dienovereenkomstig is de vraag naar specialistische vaardigheden zoals software-ontwikkeling en klantenservice gegroeid. Maar deze voordelen zijn niet zonder nadelen, zoals de gemakkelijke toegang leidt tot zorg over gokverslaving en de bijbehorende sociale en psychologische problemen. In Kentucky is de gokindustrie een belangrijk onderdeel van de economie, met de wereldberoemde paardenrennen. Technische samenwerking met Nederlandse bedrijven heeft de sector verder gemoderniseerd en de arbeidsmarkt gediversifieerd en nieuwe kansen voor de lokale bevolking gecreëerd. Maar de groei van de industrie leidt tot vergelijkbare uitdagingen als in Nederland, zoals gokverslaving en impact op kwetsbare groepen. Sociale problemen en oplossingen sociale groeivoordelen veroorzaakt in zowel Nederland als Kentucky een golf van gokgerelateerde problemen. Er zijn uitdagingen, zoals verslaving en financiële schulden. In Nederland is er een verband tussen overlast en problemen met sociale gezondheid aanwezig, zoals slaapstoornissen en sociale activiteitenvoorspeller ideaal met andere ziekte. Oplossingen zijn een gecombineerde benadering van de gokindustrie zelf, overheidsinstanties en zorgverleners, en maatschappelijke organisaties. Men kan gedacht als oplossingen aan bewustwording en preventie die de mensheid helpen om te weten over de gevaren en hardere toezicht en regelgeving van online gokplatforms die toegang voor kwetsbare groepen voorkomt. In Kentucky kan men verantwoordelijk gokken in de paardenrennensector ontwikkelen om de genoemde armoede op te lossen. Evt. programma met mensen die symptomen van neiging tot gokverslaving hebben. Dit is een uniciteit en om helpt met de bewustwording dat helpt om met Gokken te weten welke gevaar oplever. Samenwerking Nederland en Kentucky in technologie en gokken biedt economische en innovatie kansen. Dit zijn potentieel positieve toekomst maar het is belangrijk om te regelen de industrie zodat de schade wordt zo min mat ingevoerd voor gemoeid.
Toekomstige trends en ontwikkelingen
De gokindustrie in Nederland bevindt zich in de aanloopfase van aanzienlijke veranderingen als gevolg van technologische innovatie en de voortdurend veranderende regelgeving. In dit opzicht onderzoeken we de toekomst van de arbeidsmarktvooruitzichten in Kentucky en de gokindustrie in Nederland en overwegen we nieuwe vormen van samenwerking en groei. Voorspellingen voor de Nederlandse gokindustrie zijn als volgt:
- Ze digitaliseren en adopteren technologisch: op zoek naar ongeëvenaarde virtualiteit en realiteit in online gamen. Ik denk dat dit het meest toonaangevend zou zijn in de afbraak van fysieke grenzen tussen virtualiteit en realiteit en de invoering van overweldigende virtualiteit in gamen.
- Veiligheid en legalisatie: nu Nederland het online gokken recent heeft gelegaliseerd, dingen om een veiliger speelveld voor gokkers te ontwikkelen, waardoor het gebruik van meer geavanceerde technologieën wordt gemakkelijker om het spelerspubliek tegen onregelmatigheden en verslaafden te beschermen.
- Internationale samenwerking: evenzo de opkomst van buitenlandse online kansspelbedrijven, Nederlandse gokspecialisten kunnen samen met buitenlandse providers werken om andere innovaties en kansen te creëren en de groeiende markt te verpesten.
- Duurzaamheid en verantwoordelijkheid: hoe meer de gokindustrie stijgt, hoe duurzamer het segment en duurzame verantwoordelijkheid die eraan verbonden is. Bovendien zouden bedrijven gokprogramma’s opmerkelijk veel interesse steken om gokkers te helpen hun inzet te beperken en om de gemeenschap aan de linkerkant te ondersteunen.
Voorspellingen voor de Arbeidsmarkt in Kentucky
- Technologische vooruitgang en IEEE – samenwerking in de technologie tussen Kentucky en Nederland, inclusief de gokindustrie zou de verwachting zijn om nieuwe banen te openen in beide landen. Dit omvat met name de kansspellenmarkt en aanverwante technologieën zoals IT’s, cyberveiligheid en klantenservice.
- Onderwijs- en studentenuitwisseling – door lokale studenten- en uitwisselingsprogramma’s en combinatielessen uit te breiden, samenwerkingen inclusief gokken specialismen, de arbeidsmarkt in Kentucky opent voor innovatie en maakt het rondreizen uniek voor de kansspelmarkt.
- Innovatie en bereik voor buitenlandse cultuur – als gevolg daarvan met een voortdurende internationale uitwisseling van de samenwerking van Kentucky en Nederland, zal de kansspelmarkt frequenter worden. Het zal ook innovatie surfen die van beide groei ontwikkelaars in elke branche slimme technologieën meenemen.
Aan de Andere Kant zijn Nieuwe Samenwerkingsgebieden
- Gezamenlijke technologische innovatie
- Duurzaamheid in kansspel
- Onderwijs- en trainingsscholen
Aangezien de nabije toekomst veelbelovend is voor de kansspelsector in Nederland en de arbeidsmarkt in Kentucky, kijk uit naar fenomenale verbetering. Door technoFuture Direction, veiligheid, duurzaamheid en internationale verwachtingen benader te benaderen, zullen beide partijen wanneer er meer kansen zijn in de ik-industrie.
Conclusie
Reflecterend op de verbinding tussen Kentucky en Nederland, is het duidelijk dat de interactie tussen ende toekomst voor de gokindustrie. De sleutel tot succes ligt in het balanceren van economische voordelen met sociale verantwoordelijkheid, het bevorderen van internationale samenwerking, en het aanpassen aan de veranderende behoeften van consumenten en samenlevingen.
De verbinding tussen Kentucky en Nederland, hoewel misschien onverwacht, heeft bewezen een vruchtbare grond te zijn voor wederzijdse groei en ontwikkeling. Door voort te bouwen op deze fundamenten, kunnen beide regio’s de voordelen van hun unieke samenwerking maximaliseren en een voorbeeld stellen voor de wereldwijde gokindustrie. De toekomst van arbeid en gokken, met Kentucky en Nederland aan het roer, belooft een spannende reis te worden vol innovatie, uitdagingen en kansen.
Referenties
Al met al, terugkijkend op de verbinding tussen Kentucky en Nederland, kan worden gesteld dat hun interactie tussen het verleden en de toekomst ligt. Het verenigen van economische voordelen en sociale verantwoordelijkheid, bevorderen van internationale samenwerking, en zich aanpassen aan de veranderende behoeften van consumenten en samenlevingen zijn cruciaal. De relatie tussen beide locaties, ogenschijnlijk onverwacht, fungeert als vruchtbare grond voor wederzijdse groei en ontwikkeling. Door te investeren in deze connectie voor de toekomst, zullen beide partijen maximaal profiteren van hun unieke interactie en als voorbeeld dienen van hoe dergelijke partnerschappen kunnen bloeien in de mondiale gokindustrie. De toekomst van de werkplek en de gokindustrie, waar Kentucky en Nederland de weg wijzen, zal nieuw zijn en vol innovatie, uitdagingen en kansen.
Referenties In deze sectie wordt een grondige lijst van alle gebruikte bronnen en literatuur samengevat tijdens het opstellen van dit document. Deze bronnen kunnen immers verder te werk gaan met alle aangelegenheden die in eerdere secties zijn aangesneden, waaronder interactie tussen gokken en arbeid, specifiek in Kentucky en Nederland, en de aspecten van de regio’s samen. Deze publicatie beschrijft de geschiedenis van gokken in het land, inclusief de wetgeving en economische overwegingen. Deze onderzoeksrapport verkent de economische invloed van de gokindustrie op de werkgelegenheid, met inbegrip van Kentucky en Nederland, en de regionale kenmerken, die traditioneel niet verbonden waren met gokken Deze studie, zoals afgeleid uit de naam zelf, houdt verband met de technologische ontwikkelingen binnen de gokindustrie, evenals de historische en toekomstige banden van Kentucky en Nederland in dit verband. Dit document is een aanvulling op de vorige en probeert aan te tonen hoe regionale dynamiek van interactie tussen Kentucky en Nederland de economie en de gokindustrie in het bijzonder heeft beïnvloed De resterende twee bronnen, alsmede extra literatuur en onderzoekinformatie, omvatten academische tijdschriften en sites van overheidsinstanties die beschikbare beleidsinformatie over de gokactiviteiten van twee deelnemers bevatten. Dit is een beperkte lijst.
